在现代制造业中,工厂设备的实时监控和预警系统已经成为优化生产流程、提高效率的关键。一项调查指出,拥有完善监控和预警系统的企业,其设备故障率降低了20%以上。可视化工厂设备监控功能不仅能够提供实时数据,还能通过图形化界面直观地展示设备状态。这为生产管理者提供了无与伦比的便利,使他们能够迅速做出明智的决策。然而,许多企业仍在探索如何有效地实施这些功能,以最大化收益。本文将深入探讨可视化工厂设备监控的功能及实时预警方法的实现。

🚀 一、可视化工厂设备监控功能的关键要素
可视化工厂设备监控功能不仅仅是简单的数据显示,而是一个集成多种技术和功能的复杂系统。其核心在于通过视觉化工具,使管理者能够一目了然地掌控全局。
1. 数据收集与集成
在实现设备监控功能时,数据收集与集成是首要任务。数据来源的多样性和实时性决定了监控系统的有效性。
- 数据来源:可包括传感器数据、生产线数据、历史维护记录等。
- 集成技术:需要使用API、IoT协议等技术,以确保数据的无缝传输和整合。
数据类型 | 来源 | 集成技术 |
---|---|---|
传感器数据 | 设备传感器 | IoT协议 |
生产线数据 | 工厂管理系统 | API接口 |
维护记录 | 维护管理系统 | 数据库连接 |
通过准确的数据收集,监控功能能够提供精准的设备运行状态。FineVis在这一方面表现突出,其便捷的拖拽功能能够快速集成多种数据源,实现高效数据可视化。
2. 实时数据可视化
实时数据可视化是监控系统的核心功能之一,通过直观的图形、图表展示设备实时状态,使管理者能够快速识别潜在问题。
- 图表类型:包括折线图、柱状图、仪表盘等,可以根据不同的数据类型选择合适的图表。
- 可视化界面:大屏展示、PC端和移动端的多端适配,使得管理者能够随时随地查看数据。
实时数据可视化不仅提高了信息传递的效率,还增强了数据的易读性,使管理人员能够在复杂的数据间快速找到关键信息。
3. 历史数据分析与对比
通过历史数据分析,管理者可以发现设备运行的长期趋势,从而进行更有效的预测和决策。
- 数据存储:需要一个强大的数据库来管理和存储历史数据。
- 数据分析:机器学习算法和统计分析用于识别趋势和异常。
这一功能允许企业对设备的过去表现进行详细分析,从而优化未来的维护策略,提高设备的使用寿命。
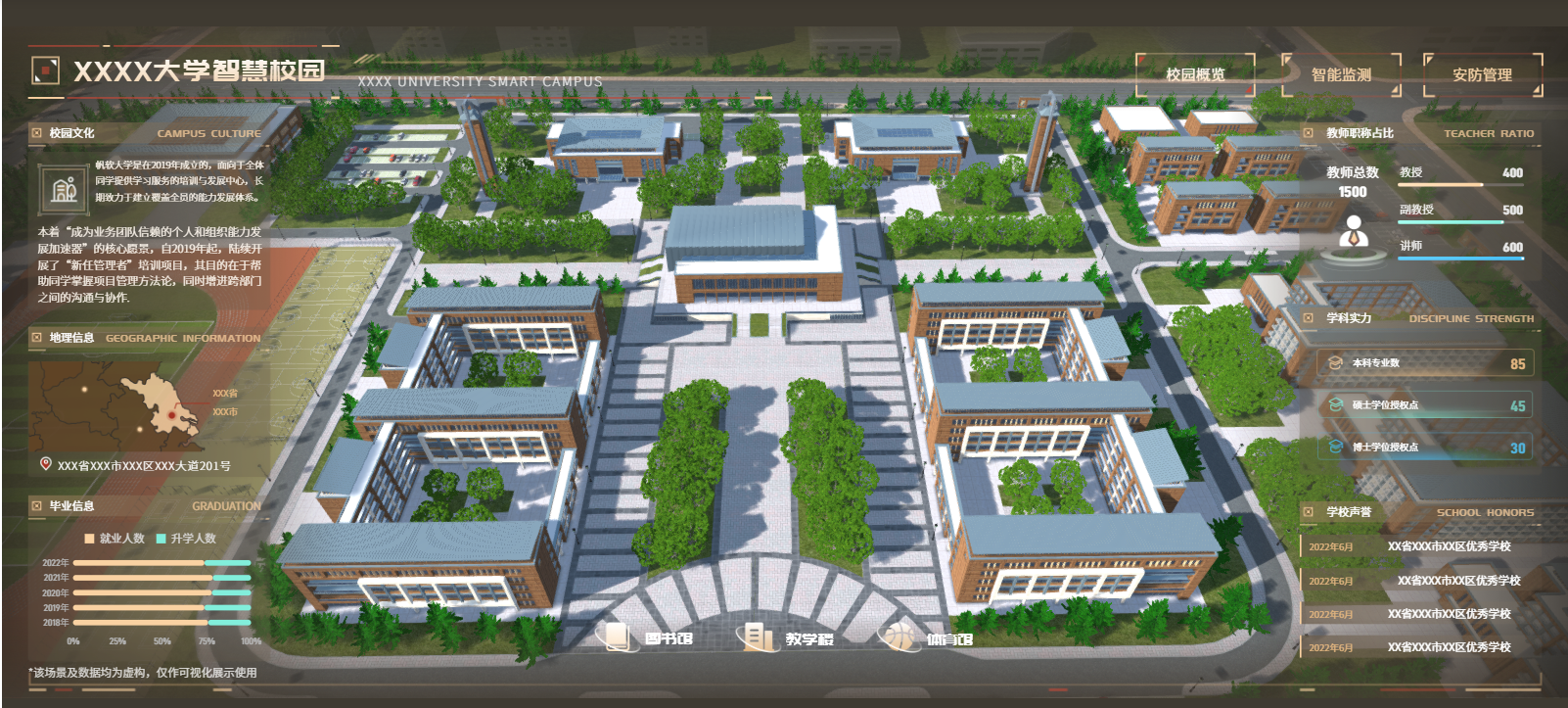
🚨 二、实时预警方法的实现与优化
实时预警是设备监控系统的另一核心功能,旨在通过预测和识别潜在问题来减少设备故障和停机时间。
1. 预警规则设定
预警系统的有效性取决于预警规则的准确性和灵活性。
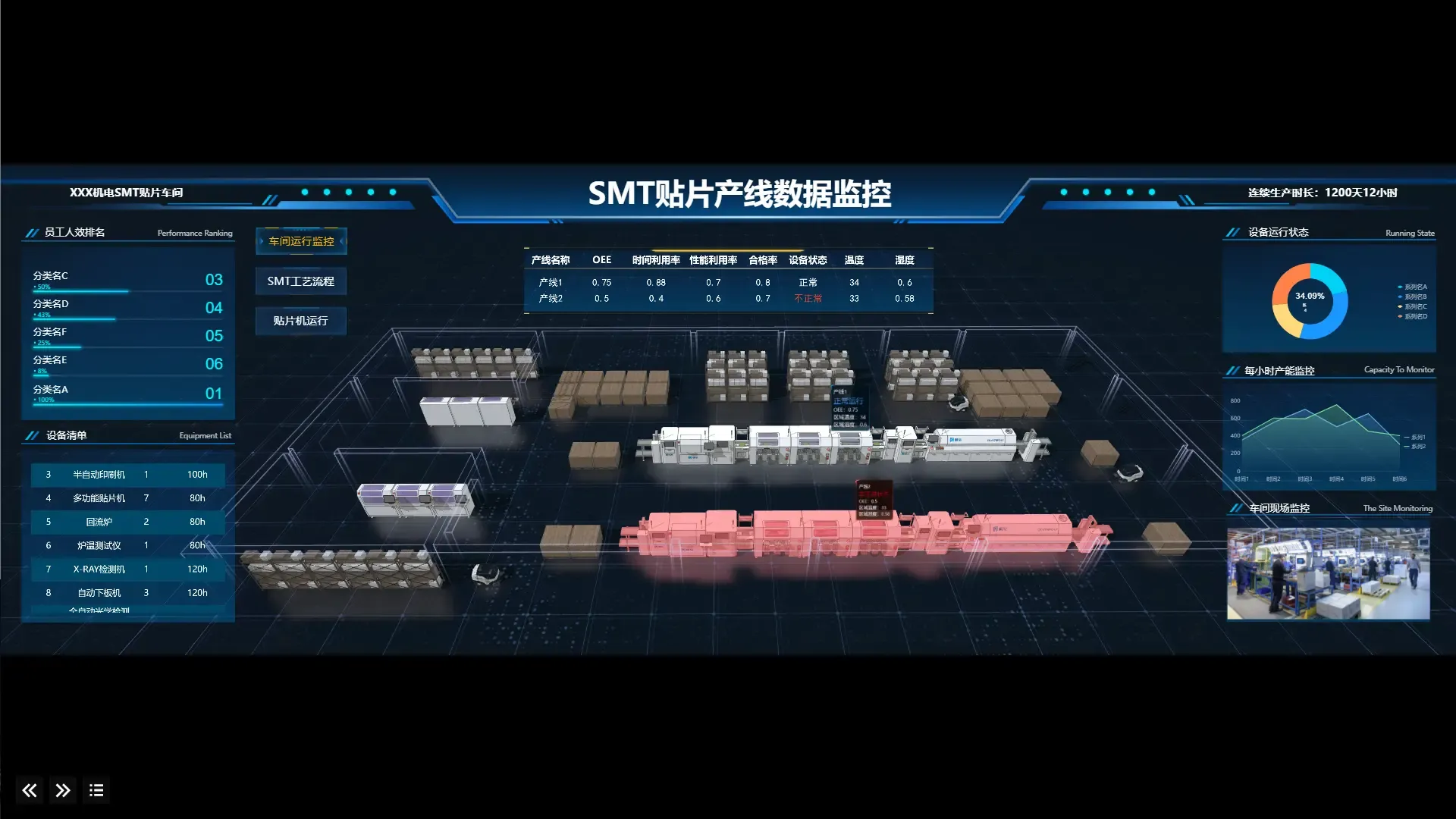
- 规则设定:根据设备类型、运行环境设定不同的预警阈值。
- 灵活调整:实时调整预警规则以适应不断变化的生产环境。
设备类型 | 预警参数 | 阈值设定 |
---|---|---|
压缩机 | 温度 | >75°C |
传送带 | 速度 | <10m/s |
加工机床 | 振动频率 | >50Hz |
通过合理的规则设定,企业能够及时识别问题,避免设备损坏或生产中断。
2. 预警通知机制
一旦预警条件触发,系统需要通过高效的通知机制将信息传达给相关人员。
- 多渠道通知:短信、邮件、应用内通知等多种方式。
- 通知优先级:根据问题的严重程度设定不同的响应优先级。
通知机制的有效性直接影响问题的解决时间,从而对生产效率产生重大影响。
3. 反馈与优化
系统运行后,及时的反馈和优化是提高预警系统准确性和可靠性的关键。
- 反馈回路:收集用户反馈和系统日志以改进预警规则。
- 持续优化:基于反馈进行持续的系统优化,确保预警的高效性。
这一过程能够帮助企业不断提高监控系统的智能化水平,使其更具前瞻性和适应性。
📚 结语
通过深入探讨可视化工厂设备监控功能及实时预警方法的实现,我们了解到一个高效的监控系统不仅能够提高生产效率,还能通过实时预警减少设备故障带来的损失。FineVis作为一款强大的可视化工具,能够帮助企业快速构建直观、易用的监控系统,满足多种场景的数据可视化需求。未来,随着技术的不断进步,监控系统将变得更加智能化,帮助企业实现更高效的生产管理。
参考文献:
- "工业4.0与智能制造技术" - 李明
- "数据可视化理论与实践" - 张伟
- "现代设备维护管理" - 王强
本文相关FAQs
🚀 如何快速搭建工厂设备的实时监控系统?
最近老板要求我们团队搭建一个实时监控系统,用于工厂设备的状态监控。但我们这边技术资源有限,想知道有没有简单易用的工具,可以快速实现这个功能?有没有大佬能分享一下经验?
在现代化工厂中,实时监控设备状态是提高生产效率和预防故障的重要手段之一。但对于许多公司来说,构建这样的系统可能面临技术资源不足的问题。幸运的是,市面上有一些工具可以帮助企业快速搭建这样的系统。其中,FineVis作为一款零代码的数据可视化设计工具,提供了一个便捷的解决方案。
FineVis能够让用户通过简单的拖拽操作创建出功能强大的可视化看板。它内置了多种图表类型和样式,包括实时三维模型和监控视频等功能,特别适合用于工厂设备的实时监控。此外,FineVis支持自适应模式,能够在大屏、PC端和移动端等多种设备上完美展示。
搭建监控系统的首要步骤是确定需要监控的设备和参数,例如温度、压力、运行状态等。接下来,使用FineVis的拖拽功能,选择合适的图表和监控组件,将这些参数可视化。通过FineVis的实时数据更新功能,可以实现设备状态的实时监控。
为了确保监控系统的稳定运行,企业还需要设置合理的数据更新频率和网络连接。FineVis支持与多种数据源连接,包括数据库、API等,确保数据的及时性和准确性。这些功能使得FineVis成为一个强大的工具,帮助企业在短时间内搭建起一个功能完善的设备监控系统。
想要体验FineVis的强大功能,可以点击这里: FineVis大屏Demo免费体验 。
⚙️ 实时监控系统如何实现设备故障的预警?
我们工厂最近频繁出现设备故障,造成了生产停滞。有没有什么方法可以在设备故障前及时预警?想了解实时监控系统在这方面能发挥什么作用。
设备故障的及时预警是每个工厂希望实现的目标,因为这将显著减少停机时间和生产损失。实时监控系统的一个核心功能就是通过分析设备的运行数据来预测潜在的故障。
实现设备故障预警需要从多个方面入手。首先,企业需要收集设备的历史数据和实时运行数据,包括温度、振动、压力等参数。这些数据通常会通过传感器实时采集,并传输到监控系统中。
其次,利用数据分析和机器学习算法对这些数据进行深入分析。例如,通过对比历史数据和实时数据的变化趋势,监控系统可以识别出异常模式,并发出预警信号。FineVis在这方面提供了强大的数据分析功能,它可以与现有的数据分析平台集成,帮助企业实现故障预警。
此外,FineVis的实时更新和自适应显示功能,可以将预警信息实时传递给相关人员,确保他们能够迅速采取措施。这种实时预警机制不仅提高了设备的可靠性,还能最大限度地保障生产的连续性。
要实现高效的故障预警,企业还需要不断优化数据采集和分析模型,FineVis的灵活性和强大功能为此提供了良好的支持。
📊 如何优化已有的设备监控系统以提升预警准确性?
我们公司已经有一个设备监控系统,但预警的准确性不高,常出现误报或者漏报现象。有没有优化的方法可以提高系统的预警准确性?
拥有一个设备监控系统是实现设备故障预警的基础,但要提高预警的准确性,这个系统需要不断优化和调整。误报和漏报现象通常由数据采集不准确、模型不完善和分析方法不当等原因造成。
首先,检查数据采集的准确性。确保传感器的精度和可靠性是减少误报和漏报的第一步。如果发现传感器数据不稳定,可能需要进行校准或更换设备。
其次,优化数据分析模型。误报和漏报可能是因为使用的分析模型不够精确。通过引入更先进的机器学习算法,并结合历史数据进行模型训练,可以提高预警的准确性。FineVis可以与多种数据分析工具集成,帮助企业利用最新的分析技术提升预警效果。
最后,考虑用户反馈和系统调整。收集使用者的反馈信息,了解预警系统在实际应用中的问题,是优化系统的重要手段。通过FineVis的灵活配置,企业可以快速调整监控参数和预警阈值,以适应实际生产环境的变化。
在不断优化监控系统的过程中,FineVis不仅提供了强大的技术支持,还提供了便捷的可视化设计平台,使得系统的调整和优化更加高效和直观。